Technical Service & Troubleshooting
We welcome telephone consultations and offer FREE advice. Our fee-based Technical Service provides on-site evaluations and in-depth analysis.
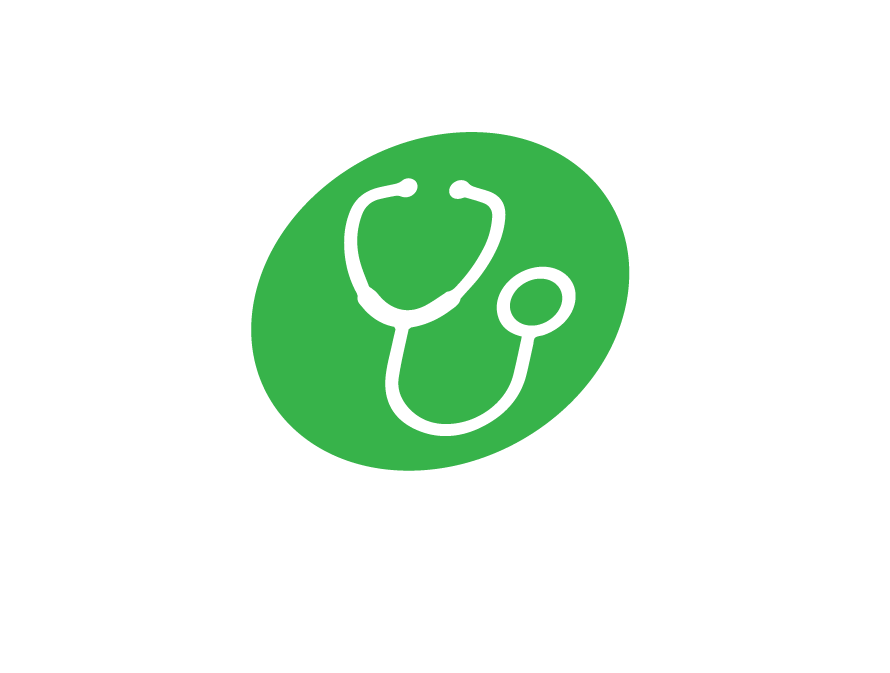
Common Problems
Possible Cause | Solution |
---|---|
Malfunction of bag cleaning System | Check all cleaning system components |
Ineffective cleaning | Modify cleaning cycle |
Re-entrainment of dust in collector due to low density material or inleakage at discharge | Check discharge valves Lower A/C Ratio |
Wetting of bags | Control dew point excursions Dry bags with clean air Clean bags or replace |
Too high A/C ratio | Verify gas volume |
Possible Cause | Solution |
---|---|
Lines(s) plugged | Blow back thru lines Protect sensing point from dust or water build-up Incorporate auto-purging system in sensing lines If copper lines – air purge them yearly – could get moisture trapped |
Manometer line(s) broken or uncoupled | Inspect and repair |
Possible Cause | Solution |
---|---|
Bag permeability increase | Test bag Check cleaning energy/ cycle and reduce if possible |
Clean to dirty plenum leakage | Inspect and repair |
Change of inlet conditions | Test & Review |
Possible Cause | Solution |
---|---|
High pressure drop across the bag house | See “High Collector Pressure Drop” above |
Low system fan speed | Check drive system increase speed |
Improper duct balancing | Rebalance system |
Plugged duct lines | Clean out |
Poor hood design | Evaluate temporary modifications and implement |
Possible Cause | Solution |
---|---|
Inleakage at discharge points | Inspect and repair seals or valves |
Malfunction of discharge valve, screw conveyor or material transfer equipment | Inspect and repair |
Re-entrainment of dust with in collector | Check for leaks at discharge or hopper |
Retainment of dust on filter bags | Increase cleaning |
Possible Cause |
---|
Improper paint material or Application |
Improper insulation |
Emission of nearby equipment |
Dew point excursions |
Improper shutdowns |
Possible Cause |
---|
Vibrations or banging of moving parts |
Squealing of belt drives |
Dust Collector Maintenance
Maintain daily pressure drop readings on graph |
Keep bag location replacement chart |
Watch for consistent bag failures and retain typical bag for inspection |
Retain bags that have unusual or noncharacteristic failures |
Maintain an adequate supply of bags, cages and Diffusers to avoid costly production delays |
Check pressure drop across baghouse |
Check header air pressure |
Drain header |
Check air lock for operation and leaks |
Rap hopper with rubber hammer to avoid bridging and build up |
Visually inspect stack |
Check temperature gauges (know bag limitations: temperature) |
Inspect tubesheet for dust accumulation, corrosion and evidence of condensation |
Visually inspect bags for blinding, leakage and wear. When possible perform Trace-It leak detection test |
Check timer control for operation and proper pulse sequence and duration |
Clean pressure gauge taps with compressed air |
Check foundation bolts, housings and belts on fans and motors |
Check inlet air flow into baghouse |